Obsolescence Management for Electronics
Obsolescence Management for Electronics
5 Ways to Be Proactive When It Comes to Obsolete Parts
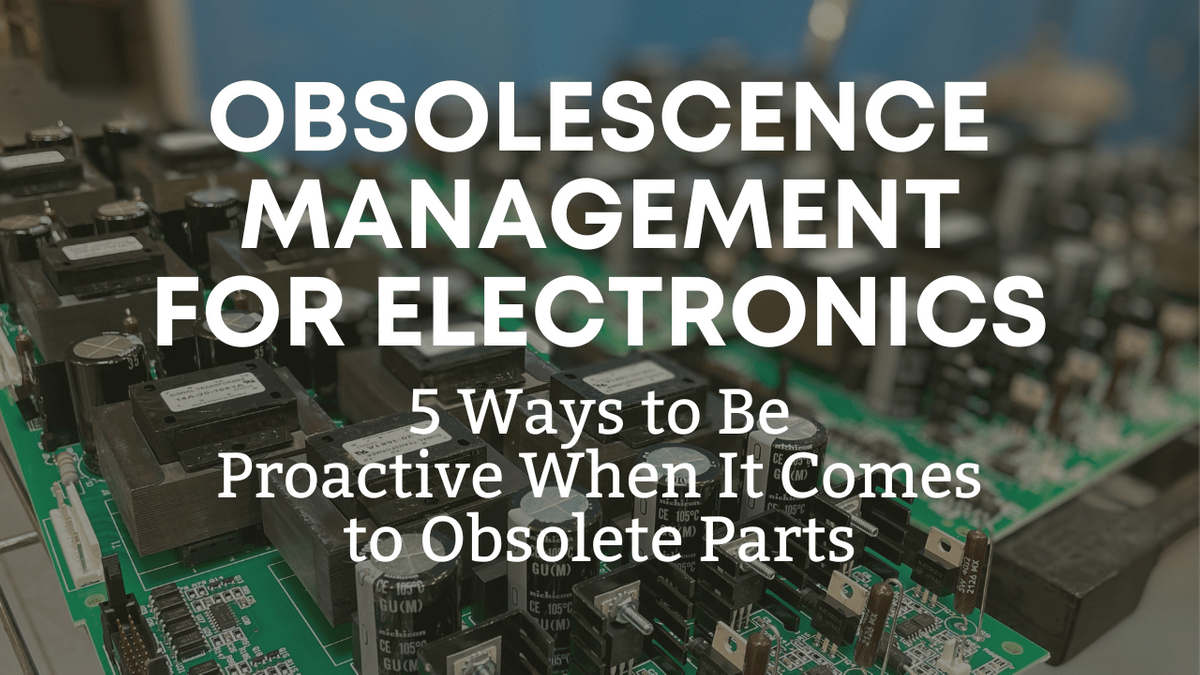
As a printed circuit board (PCB) begins to age, some components on the board may no longer be available for purchase as replacements. Obsolescence occurs when a PCB or other electronic product has components that are beyond the point of repair or replacement, potentially putting the whole system at risk of dysfunction.
Obsolescence management for electronic components is one of the most important stages of a PCB’s life. It’s an integral process for ensuring you get the most out of your PCB investment.
Passive and Active Part Obsolescence
Components in a PCB build are typically considered either “passive” or “active” components. Passives make up the majority of a PCB system; these would include resisters, capacitors, etc. and are easier and less expensive to replace.
Active components are the ones the PCB can’t live without, such as integrated circuits or transformers that function as the “brains” of the board or PCB assembly. They are often more expensive and much more difficult to replace, especially when they become obsolete.
Part Obsolescence: Five Ways to Be Proactive
A common risk involved with aging parts is that replacements are no longer produced or have compromised quality. It is important to be proactive in order to stay ahead of the game, particularly with those active components that are essential to the performance of your PCB.
Here are five reasons why you should be proactive when it comes to obsolete parts…
- Avoid “Line Down” Situations. Line down issues on any product line are traumatic, especially if you’re the one purchasing and managing the parts. If just one sub-component is not ready, the whole production line comes to a screeching halt, hence “line down.” Time is money; every minute your line is down, dollars are being lost.
- Keep Your People Busy. Your employees showed up to work this morning, but if an obsolete part has stalled production, not only are you losing money because the product isn’t coming off the line, but you’re also paying your people to sit around and wait for the replacement part to come in.
- Maintain Original Design and Flow. When a specified component isn’t available, the function of the board can be compromised. Electronic engineers select certain parts because of the critical role they play in the function of a PCB. One obsolete part could result in a domino effect of multiple components failing.
- Save Money. What we learned about supply and demand in high school comes into play here. As a component becomes more scarce (obsolescence), its price increases. And, if you cannot find it, the cost of redesigning a board because of an obsolete part can be even more expensive.
- Preserve Quality. When faced with an unexpected situation related to part obsolescence, the typical response is to rush to fix the problem. This means skipping essential steps in the process, such as prototyping and quality testing to see if the “fix” actually works at the same level of the original.
Have a Plan.
Now that you know WHY you need to be proactive, let’s discuss HOW to make sure you have a plan for obsolescence management for electronic components.
- Designing for Manufacturability: It starts at the beginning. When designing and engineering your PCB, a good contract manufacturer will not only consider the steps to make a better product at a lower price; he or she will offer insight on parts that might be obsolete in the near future and/or difficult to source.
- Relationships: In a recent blog post, we discussed how strong relationships can positively affect supply chain management. The same is true for obsolescence management for electronics components. Finding a PCB manufacturer that brings to the table relationships with more than one source for parts ensures you won’t be stuck with only one supplier. Plus, a PCB company who works with a network of suppliers can also obtain better pricing on components on the open market.
- Open Communication: Your contract manufacturing partner should remain in close contact with you AND the OEMs and suppliers of components used in your PCB build. When done effectively, this ensures that you can take advantage of “last-time buys” in advance of a part becoming obsolete. Working together, you can also create just-in-time manufacturing solutions that will make certain you have enough stock in place to continue to deliver your product even if a component does become obsolete. Then, you’ll have the time to source the component, find a replacement, or design a new solution.
The bottom line is that your electronics contract manufacturer (ECM) should provide you with valuable information about potential component sourcing news and suggest engineering solutions to obsolescence.
How Can We Help You?
Are you looking to improve your printed circuit board assembly or box build? Or maybe you’re in the early stages of a new product design? If so, request a free project review today, and we’ll reach out to you to learn more about your need.
If you’re not quite ready for a full quote, try a free “Snapshot Analysis” of your current board or initial drawings. We’ll take a look and give you our thoughts based on more than 100 years of combined experience.
In the end, quality is our focus. We hope to hear from you soon.